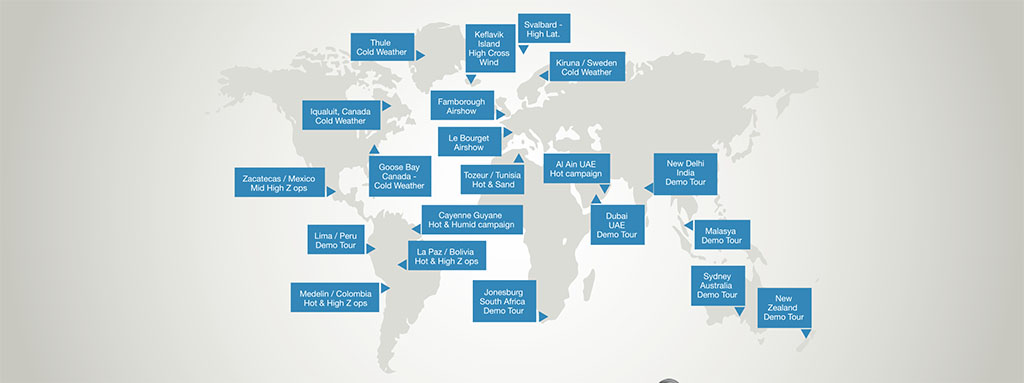
Manufacturing engineering
Technical consultancy / Operations
Date: 2009-ongoing
Client: AIRBUS Defense & Space
The service has been outsourced. AERTEC’s PMOs are therefore located at the client’s facilities and integrated into the work teams. Services:
¬ Logistical coordination for all aircraft for any need
¬ Requesting the procurement manager for delivery of equipment/parts needed for the aircraft
¬ Attending weekly A400M programme meetings (in headquarters), where claims, returns and any equipment changes in aircraft are coordinated
¬ Attending daily MSN 2 and MSN 4 industrial meetings
¬ Coordinating the different departments (production, configuration quality, manufacturing engineering, etc.) to ensure urgent flows are correctly dealt with in SAP
¬ Returning equipment and parts to the Procurement Manager
¬ Managing flows of materials between FAL in Seville and FTC in Toulouse: testing tools and instrumentation, equipment located in the Toulouse spare parts warehouse, loans and cannibalised parts
¬ Preparing all the logistics for campaigns abroad (Sweden, Peru, South Africa, Asia, etc.): spare parts in the aircraft (fly-away kit), necessary tools, transport, customs, AOG (aircraft on ground) during campaigns or testing: special transport, cranes, awnings, etc.
¬ Providing FTC Toulouse with support for anything they may have from Seville
¬ Coordinating all transfers of the materials needed when MSN2 or MSN4 go to Toulouse
¬ Managing shipments in means of transport to and from Toulouse and Seville on a daily basis
Work phases
¬ Initiation: Identification of the requirements and analysis of possibilities for completion
¬ Development: Carrying out planned tasks. Monitoring and reporting the progress of activities
¬ Closure: Formalising the project’s closure
Scope of work
¬ Providing support to the aircraft team manager and operational managers regarding each aircraft’s day-to-day needs
¬ Attending periodic monitoring meetings and programme status reporting
¬ Setting the main KPIs
¬ Hangar layouts
¬ Monitoring and distribution of the stock of wheels, rims and tyres
¬ Inventory review of flight test equipment warehouse
¬ Checking regularisations made by Toulouse
¬ Monitoring GSE files and tools loaned and received by the FTC
¬ Checking FTA
¬ Checking equipment in MRSA
¬ Checking stock, older than a month, in LTK aircraft materials hangar
¬ Maintenance analysis and subsequent actions
¬ Checking stock of consumable materials for AyG
¬ Reviewing outstanding points with Coordination’s support
¬ Closing orders
¬ Drawing up master list
¬ Drawing up EDTF report
¬ FTC e-room stock
¬ Preparing retrofit meetings
¬ EDTF meetings, minutes and actions
¬ Retrofit meetings, minutes and actions
¬ Attending interdepartmental N3 meetings
¬ Attending MSN2 industrial meetings
¬ Attending MSN4 industrial meetings
¬ Attending N1 meetings
¬ Taking part in lean manufacturing enhancement projects
¬ Reviewing working parties’ SIs